A 3D printer uses a variety of plastics or resins to build a physical model from a virtual design on a computer. The model is then “sliced,” dividing it into hundreds or even thousands of layers that are fed to the machine one at a time.
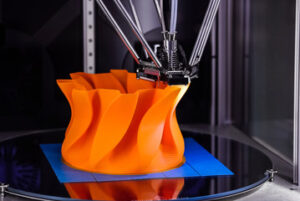
This process varies by technology, from desktop printers that melt a plastic material to metal 3D printing methods like electron beam melting or direct metal laser sintering. These technologies can produce complex and dense objects. Visit https://www.by3design.com/ to learn more.
Additive manufacturing (AM) is a fabrication process that builds objects in layers. It can be used to create a wide variety of products, from medical implants to car parts to architectural models. AM is preferred for rapid prototyping and small-scale production because it is faster, more accurate, and generates less waste than conventional fabrication techniques.
The Library’s 3D printers use a variety of different plastics or resins to build real, physical models from virtual 3D designs. Patrons may either design their own models using free, easy-to-use software like TinkerCad or download and print a model from an online repository like Thingiverse. The Library is not able to provide assistance with the design of your models, but staff can help with basic equipment and software support.
GE’s successful production of 100,000 parts with AM technology in 2021 was a milestone for the industry, proving that additive printing is ready for commercial use. AM can produce complex, customized parts on short notice and with little to no assembly required. It also reduces costs by eliminating the need for costly tooling and milling and generating less waste.
The most common type of 3D printing is called fused filament fabrication, or FFF, which uses a material extrusion technique. It feeds thermoplastic materials from a coil or spool into the printer, where the print head heats them up until they melt. The melted material is then deposited on a platform in layers to form the desired object. The material is typically plastic, but it can be other materials as well. This is one of the cheapest forms of additive manufacturing. Other methods of 3D printing include stereolithography and selective laser sintering.
Additive design
Design for Additive Manufacturing (DfAM) is the process of adapting a product’s design to take advantage of the strengths of 3D printing. The goal is to produce a final part that will be both functional and easy to manufacture. This requires a great deal of expertise, and engineers must often make trade-offs when designing for additive technology.
A key consideration in DfAM is tolerance. This is the extent to which a printed object matches its digital model, or in other words, how close the print is to its intended shape and dimensions. Tolerance is usually influenced by the 3D printer’s build process and hardware, including its nozzle size and accuracy. Tolerance is also determined by the material used and its physical properties.
Another consideration is support structure placement. Most types of 3D prints require support structures to keep the part from warping or drooping as it is being built. These supports are then removed after the print is complete, but they can increase the cost of a finished part. To minimize the need for support structures, engineers can reduce the size and thickness of the parts they are producing, change their orientation, or use dissolvable supports.
Lastly, designers can optimize their designs for function by making them lighter and stronger. This can help them reduce assembly processes, improve quality and performance, and reduce the cost of production. There are several software packages that can help designers achieve these goals, including nTopology and Altair.
Additive design can be applied to a wide range of industries and products. For example, it can be used to customize consumer products to match the physiology of the wearer, reduce material waste, and streamline supply chains. It can also be used to enhance functionality, reduce weight, and create aesthetically-pleasing organic shapes.
3D modeling software
The 3D printing process creates a physical object from a digital model. The process can range from simple desktop printers that melt plastic over a print platform to large industrial machines that use lasers to selectively melt metal powder at high temperatures. The resulting print is then post-processed to reach the desired final appearance. The entire process takes about an hour or more to complete. The print begins as a virtual 3D design file created using Computer Aided Drafting (CAD) software or downloaded from an online repository. The digital model is then sliced into thin layers that the printer can build up over time. The layers are then printed one at a time, usually in a plastic material. The slicing process can be customized to optimize print quality and speed.
Among the top-rated 3D modeling software is ZBrush, which is famous for its real-time sculpting capabilities and its compatibility with pressure-sensitive pen and graphics tablets favored by concept artists and filmmakers. It also features an integrated learning library, a variety of brushes, and multiple tools for creating and editing meshes. Its user interface is designed for more experienced modelers, but it offers a wide variety of tutorials and videos for beginners.
Another great option is Blender, which can be used to create environments and characters for video games. Its mesh edit, repair, and optimization tools allow users to sculpt and re-topologize models before preparing them for 3D printing. It is also available as a free download and has an extensive user community.
Other 3D modeling software is geared toward specific industries and can be purchased or subscribed to based on the type of work required. CAD (Computer-Aided Design) software, for example, is typically used by engineers to produce 2D and 3D technical volumetric drawings. Other specialized programs, such as PartCrafter, can take 2D photographs of an object and turn them into a detailed 3D model.
Materials
Using 3D printing requires special materials to build physical objects. The material is a crucial component of the machine’s function, and different printers require specific types of material. Choosing the right material can make or break your project. Several important factors must be considered when selecting the ideal material for your design, including mechanical strength, flexibility, chemical resistance, heat tolerance, and surface finish.
There are many different materials available for 3D printing, ranging from various plastics to metals and even sand. Each material has its own unique properties and advantages. For example, polypropylene is an inexpensive, durable plastic that is used in a variety of applications, including tote bags and twine. It also offers good resistance to moisture and high tensile strength. In addition, it is very light, making it a popular choice for printed electronics and solar panels.
The choice of materials for 3D printing is not only influenced by the specific requirements of the design, but also by the technology used in the printing process. For example, a fused filament fabrication (FFF) 3D printer uses a type of heated plastic to create the object’s layers. Alternatively, stereolithography (SLA) technology uses a computer-controlled UV laser to trace patterns on a liquid resin and cure it layer by layer.
Among the most popular 3D printer materials is nylon, which has excellent strength and durability. It is especially useful in printing functional prototypes and high-performance gears that require exceptional impact resistance. This material is also used to print parts with complex geometries for aerospace, automotive, and medical applications. Nylon is also available in reinforced glass forms that provide enhanced stiffness and tensile strength. It is also used in the SLS technique for printing parts that rely on consistency and durability.
Printing
3D printing is a process of turning a digital model into a solid three-dimensional physical object by adding material layer by layer. This differs from traditional machining, casting and forging processes that remove material from stock or pour into a mold to create shapes. 3D printing technology enables a wide range of users, from engineers to artists, to cost-effectively develop, customize and rapidly prototype components for their projects.
The first step in any 3D printing project is creating a 3D model using computer-aided design software, or CAD. Once the model is ready, it’s sliced into a series of two-dimensional layers that tell the printer where to solidify starting materials. This allows the printer to produce objects that are difficult or impossible to make through conventional machining, molding and casting.
Different types of 3D printing technology use various materials and platforms, but they all follow the same basic principles. For example, with fused filament fabrication (FFF) 3D printers, nozzle-type nozzles dispense material onto platforms in iterations of layers, forming the desired shape. Other print technologies like stereolithography (SLA) use liquid resins, and lasers trace patterns of photopolymers on the surface of the resin, curing them into solid objects layer by layer. Still others, like binder jetting, use powders, and a printhead sprays binder into extremely precise shapes on top of the powders to form an object.
When preparing models for 3D printing, keep in mind that the more support structure required for a model, the longer it will take to finish and how much material will be used. Keeping these factors in mind, consider reducing the amount of supports to reduce print time and material consumption. Alternatively, try printing the model without supports to make it faster and more accurate.